A costume maker who has created outfits for Aquaman and James Bond has returned to the North East to launch her own sustainable homeware business.
Rosie Bath, who has worked with some of Hollywood’s biggest stars, has swapped the film studio for her own design studio, with the launch of Cera Cotton, an award-winning homeware brand.
Based in Newcastle, Cera Cotton produces a wide range of plastic-free, vegan wax cotton homeware products and accessories, from bunting to travel kits, plant pouches and gift boxes.
Rosie set up the business after a camping trip with friends opened her eyes to the number of polluting plastics used in the manufacture of every-day travel essentials and accessories.
Using her skills as a costume maker, she began experimenting with plastic-free fabric alternatives and many prototypes and late nights later, she stumbled upon the perfect solution.
“I was going camping and wanted to make some bunting to go around the tent,” she recalls. “I noticed that there was a lot of plastic and I just thought, ‘surely there’s a better way?’
“I searched for hours online and couldn’t find anything, so I had to make do, however that was what really kickstarted everything.
“Working as a costume maker, I’d made outfits for the likes of Bridgerton, the Little Mermaid, James Bond, you name it.
“At times, this meant producing items using traditional forms of manufacture with materials which aren’t widely used today, such as wax cotton.
“I still remember the first time I used it. I was producing a wax cotton jacket and just loved working with it. Historically, British sailors used it to produce the sails on ships due to its water resistance and incredible durability. It’s a tried and tested 500-year-old fabric.
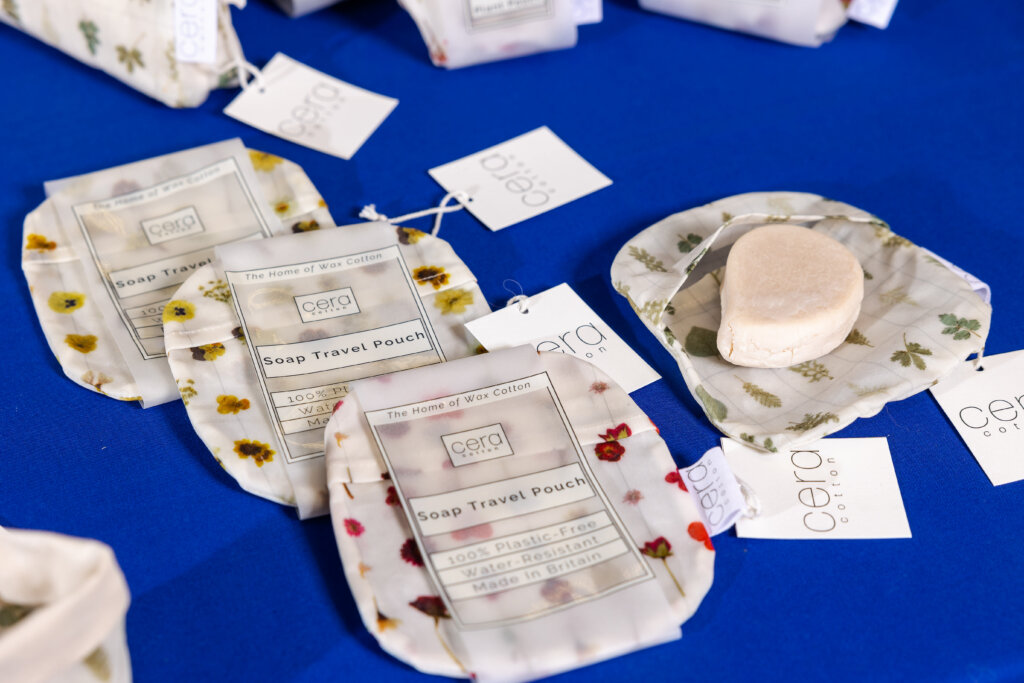
“I have a real passion for looking back at how we lived before and how we can use old materials and means of production to live better lives, without sacrificing the convenience and quality that we have today, so it was a perfect fit.”
Despite a wealth of experience in costume manufacture, Rosie had no experience of running a business and manufacturing at scale, so she sought advice from the Sustainable Advanced Manufacturing (SAM) Project at the University of Sunderland.
After attending a series of workshops to understand manufacturing best practice and how to set up a production space, she decided the time had come to up sticks and return home to the North East to finally chase her dream of becoming her own boss.
“The workshops were great,” she added. “I’d worked in London for over five years but had always wanted to set up my own business and the support from SAM really gave me the confidence that I knew this was something I could really make a success of.
“Having been born and raised in the North East and having studied fashion design at Northumbria University, I know how hard it can be to find work in the creative industries outside of London.
“I studied fashion design and marketing at Northumbria University but most of the graduates moved away to London and Manchester. If I had the chance to stay in Newcastle, I would have, but the opportunities just weren’t there, however this is something I’d love to change.”
Since the launch of its online store in August 2022, Cera Cotton has launched eight core products with more set to follow over the coming months.
The company is also exploring the idea of supplying the retail sector, with Rosie recently hosting successful pop-up stores at Boots and Harvey Nicholls.
She said: “The ultimate aim is to become the home of wax cotton. I want to be selling a wide range of products and to employ local people. I’d love to work with local universities too, to provide opportunities to other creative graduates, but we’ll take it one step at a time.
“For now, it’s about continuing to grow the business by spreading the word of what we’re doing and educating people about the benefits of buying sustainable products, and I’m confident that the pop-up stores will provide us with the perfect platform to do that.”
Neil Taylor, Automation and Robotics Specialist at the SAM Project, said: “The SAM Project was set up to help SMEs better understand the manufacturing process and Rosie is a great example of the impact the programme has had.
“As well as helping established manufacturers innovate and grow by investing in new technology and creating jobs, we’re also helping aspiring manufacturers break into the industry by ensuring companies such as Cera Cotton have access to the tools and knowledge required to get off to the best possible start. It’s been great working with them and we’d like to wish them all the best for the future.”